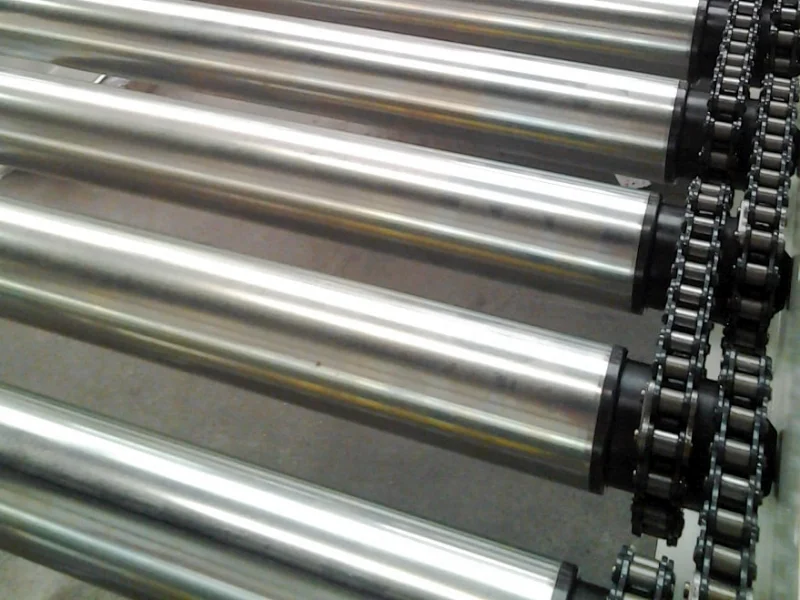
High Performance Chain Driven Roller Conveyors
Chain driven powered roller conveyors is robust and ideal for heavy-duty tasks like pallet handling or industrial transport, using roller chains to transmit power from a motor to rollers. Below is a comprehensive guide on chain-driven roller conveyors, covering their design, key components, selection process, pricing, and sourcing, reflecting the 2025 market context.
What is a Chain-Driven Roller Conveyor?
A chain-driven roller conveyor is a powered roller conveyor system that uses a motor to drive a roller chain (or multiple chains) that rotates rollers to move loads along the conveyor. The chain engages sprockets attached to the rollers, providing slip-free, high-torque power transmission. These conveyors are designed for heavy or demanding applications, such as transporting pallets, large boxes, or industrial goods, and are known for their durability and ability to handle harsh environments. We offer pallet roller conveyor and boxes roller conveyor and more roller conveyors for sale.
Key Features of Chain Driven Roller Conveyor
- Power Transmission: Chains ensure consistent, reliable movement, even under heavy loads (500–5,000 lbs+).
- Versatility: Suitable for straight, curved, or accumulation setups.
- Durability: Robust design for abrasive, dirty, or high-impact conditions.
- Applications: Warehousing, manufacturing, pallet handling, automotive, food processing (with stainless steel).
Key Components of Chain Driven Roller Conveyor
1.Conveyor Rollers
Support and move loads; driven by chains.
Specifications:
- Diameter: 1.9" (light-duty), 2.5"–3.5" (medium/heavy-duty).
- Material: Steel (galvanized), stainless steel (food-grade), or plastic (light loads).
- Spacing: 3"–6" centers; loads span 3+ rollers.
- Sprockets: Attached to roller axles, engage chain (e.g., #50 sprocket, 15 teeth).
2. Roller Chain
Transmits power from motor to rollers or between rollers.
Types
- #40 (1/2" pitch): Light/medium loads (<500 lbs).
- #50 (5/8" pitch): Medium/heavy loads (500–2,000 lbs).
- #60 (3/4" pitch): Heavy-duty (2,000–5,000 lbs).
Stainless steel or nickel-plated for washdown/corrosive environments.
Specifications
- Tensile Strength: #40 (3,700 lbs), #50 (6,100 lbs), #60 (8,500 lbs).
- Length: ~2x conveyor length (e.g., 10' conveyor ≈ 20' chain).
3. Sprockets
Engage chain to drive rollers or connect to motor.
Specifications
- Match chain pitch (#40, #50, #60).
- Teeth: 10–30 (15–20 common).
- Material: Steel or stainless steel.
4. Drive System
- Motor: Electric, 1/2–5 HP (110V–480V), drives chain via gearbox or sprocket.
- Gearbox: Reduces speed, increases torque (e.g., 20:1 ratio).
- Controls: On/off, variable frequency drive (VFD), or PLC with sensors for automation/accumulation.
5. Conveyor Frame
- Function: Supports rollers, chains, and motor; withstands load weight.
- Material: Steel (powder-coated), aluminum (light-duty), or stainless steel (food-grade).
- Width: Matches load + margin (e.g., 48" pallet + 6" = 54" wide).
- Height: 12"–36" (low-profile for pallets, ergonomic for boxes).
6. Side Rails
Guide loads, prevent derailment.
- Types: Fixed (2"–6" high), adjustable, or roller guides.
- Material: Steel, aluminum, or stainless steel.
7. Accessories
- Chain Guards: Cover chains for safety.
- Sensors: Enable accumulation or flow control.
- End Stops: Prevent loads from rolling off (gravity sections).
- Supports: Legs/stands every 5–10 feet.
Design Considerations
1. Load Capacity
- Light-duty (<500 lbs): #40 chain, 1.9" rollers.
- Medium-duty (500–2,000 lbs): #50 chain, 2.5" rollers.
- Heavy-duty (2,000–5,000 lbs): #60 chain, 3.5" rollers.
- Calculate total load (weight × items) and select chain/roller ratings.
2. Conveyor Layout
- Straight: Simple, common for pallets or boxes.
- Curved: Tapered rollers (wider outer edge) for smooth turns (e.g., 90°, 24" inner radius). Tapered roller conveyors are used in curved roller conveyor in bulk unit handling system.
- Accumulation: Our accumulation roller conveyor has Zoned chains with clutches or sensors for zero-pressure queuing.
3. Speed
- Range: 30–60 ft/min (adjustable via VFD).
- Smaller sprockets increase speed; larger sprockets boost torque.
4. Environment
- Dry/Indoor: Carbon steel chains/rollers.
- Washdown/Food-Grade: Stainless steel, sealed bearings.
- Harsh (Dust, Oil): Nickel-plated chains, heavy-duty rollers.
5. Maintenance Access
- Design for easy chain lubrication (every 100–500 hours) and sprocket replacement.
- Use removable chain guards and accessible motor mounts.
6. Safety Features
- Chain guards, emergency stops, and overload protection.
- Side rails (4"–6" high) for heavy or unstable loads.
How to Choose a Chain-Driven Roller Conveyor
1. Define Application Requirements
- Load: E.g., 1,500-lb pallets (48" x 40") or 50-lb boxes (18" x 12").
- Purpose: Transport, accumulation, or staging.
- Distance: E.g., 20' straight or 10' + 90° curve.
2. Select Chain and Rollers
Chain
- #40 for <500 lbs.
- #50 for 500–2,000 lbs.
- #60 for 2,000–5,000 lbs.
Rollers
- 1.9" for light-duty; 2.5"–3.5" for medium/heavy-duty.
- Spacing: 3"–6" (load spans 3+ rollers).
3. Choose Drive System
- Motor: 1/2 HP (light), 1–2 HP (medium), 2–5 HP (heavy).
- Controls: Basic (on/off) or advanced (PLC, sensors for accumulation).
- Speed: 30–60 ft/min, adjustable.
4. Determine Frame and Width
- Width: Load width + 4"–6" (e.g., 48" pallet = 54" conveyor).
- Frame: Steel for heavy-duty; stainless steel for food-grade.
5. Factor in Environment
- Indoor: Carbon steel.
- Washdown: Stainless steel.
- Corrosive: Nickel-plated or galvanized.
6. Budget and Maintenance
- Cost: $2,000–$15,000 per 10'–20' section.
- Maintenance: Lubricate chains monthly; inspect sprockets/rollers quarterly.
Pricing of Chain Driven Roller Conveyor
Chain-Driven Roller Conveyor:
- Light-duty (24" wide, #40 chain): $2,000–$5,000 for 10'.
- Medium-duty (36" wide, #50 chain): $4,000–$8,000 for 10'.
- Heavy-duty (54" wide, #60 chain, pallets): $6,000–$15,000 for 10'–20'.
- Example: 15' x 54" for pallets ≈ $7,000–$12,000.
Key Components:
- Rollers: Steel (2.5"): $10–$30 each; stainless steel: $20–$50.
- Chain: #50 (carbon steel): $1–$2.50/ft; #60: $1.50–$3.50/ft; stainless: $3–$10/ft.
- Sprockets: #50, 15-tooth: $10–$20 each.
- Motor: 1–2 HP: $200–$500; gearbox: $200–$1,500.
- Side Rails: Steel (4" high): $10–$20/ft.
- Spares: Budget $200–$500 for chains, sprockets, rollers per 10' section.
Maintenance Tips of Chain Driven Roller Conveyor
- Chains: Lubricate every 100–500 hours (SAE 20 oil or grease); replace if stretched >3%.
- Rollers: Inspect bearings monthly; replace if noisy or bent.
- Sprockets: Check for worn teeth quarterly.
- Motor/Gearbox: Service annually; monitor for overheating.
- Side Rails: Ensure no dents or loose bolts; clean in washdown settings.
Example Specification
- Scenario: 20' chain-driven roller conveyor for 1,500-lb pallets (48" x 40").
- Width: 54" (48" + 6").
- Rollers: 2.5" steel, 4" spacing (pallet spans 12 rollers).
- Chain: #50 carbon steel (6,100 lbs strength), 40' total.
- Drive: 2 HP motor, 40 ft/min, PLC with sensors for accumulation.
- Frame: Steel, 18" height (forklift-friendly).
- Side Rails: Fixed steel, 4" high.
- Cost: $8,000–$14,000 (conveyor); $200–$400 (spares: 10' chain, 5 rollers, 5 sprockets).
Chain-driven roller conveyors are durable, high-torque systems for heavy loads, costing $2,000–$15,000 per section. Key components include #40–#60 chains ($1–$10/ft), 2.5"–3.5" rollers, and 1–5 HP motors. Selection depends on load, environment, and automation needs. If you need a specific design, component focus (e.g., chain sizing), or pricing for a particular setup, share details (e.g., load, conveyor length), and I'll refine the response!
Leave Me Your Requirement!