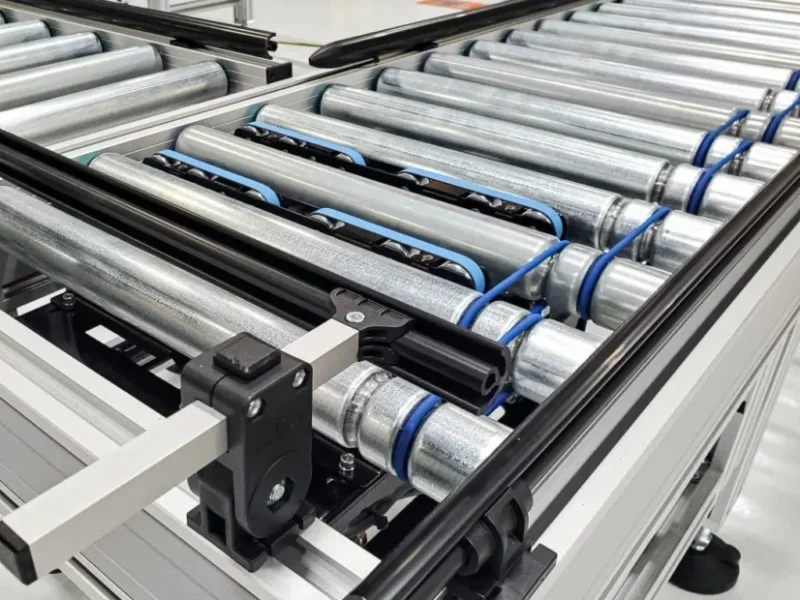
Belt Driven Roller Conveyor for Light to Medium Loads
Belt-driven roller conveyors use belts (typically flat or round) to transmit power from a motor to rollers, offering a quieter and smoother alternative to chain-driven systems, though they are less common for heavy-duty applications. Below is a comprehensive guide on belt-driven roller conveyors, covering their design, components, selection process, pricing, etc.
What is a Belt-Driven Roller Conveyor?
A belt-driven roller conveyor is a powered conveyor system where rollers are driven by a motor via belts (flat, round, or O-ring belts) that connect the motor or a drive shaft to the rollers. The belts transfer rotational force, causing the rollers to move loads along the conveyor. These systems are quieter and smoother than chain-driven conveyors and are typically used for light to medium-duty applications, such as transporting boxes, totes, or small pallets. They are less common than motor-driven (MDR) or chain-driven systems but are valued for their simplicity and low maintenance.
Key Features of Belt-Driven Roller Conveyor
- Smooth Operation: Belts provide quieter, less jerky movement compared to chains.
- Low Maintenance: Fewer lubrication needs than chain-driven systems.
- Versatility: Suitable for straight, curved, or accumulation setups.
- Energy Efficiency: Moderate power consumption, especially with modern motors.
- Applications: Warehousing, distribution, packaging, assembly lines, and light industrial tasks.
This is a roller conveyor using round belt to drive conveyor rollers.
Key Components of Belt-Driven Roller Conveyor
1. Conveyor Rollers
Support and move loads; driven by belts.Specifications
- Diameter: 1.5"–2.5" (light/medium-duty); 3.5" for heavier loads (rare).
- Material: Steel (galvanized), stainless steel (food-grade), or plastic-coated.
- Spacing: 2"–6" centers; loads span 3+ rollers.
- Drive Connection: Rollers have grooves or pulleys for belt engagement (e.g., O-ring grooves).
2. Drive Belts
Transmit power from motor or drive shaft to rollers.
Types
- O-Ring Belts: Round polyurethane belts, common in line-shaft conveyors, connect rollers to a drive shaft.
- Flat Belts: Wide, flat belts under rollers for direct drive (e.g., belt-driven live roller, BDLR).
- V-Belts: Less common, used for high-torque applications.
Specifications
- O-Ring: 3/16"–1/4" diameter, 10"–24" length (loop).
- Flat Belt: 4"–12" wide, continuous loop under rollers.
- Material: Polyurethane (durable, flexible), rubber (high grip), or PVC (food-grade).
- Tension: Adjustable via pulleys or tensioners to prevent slippage.
3. Drive System
- Motor: Electric, typically 1/2–2 HP (110V–480V), drives a shaft or belt pulley.
- Drive Shaft (Line-Shaft): Common in O-ring systems; a rotating shaft runs parallel to rollers, connected by belts.
- Gearbox: Reduces motor speed, increases torque (e.g., 10:1–20:1 ratio).
Controls:
- Basic: On/off or fixed speed.
- Advanced: Variable frequency drive (VFD), PLC, or sensors for accumulation.
- Speed: 30–150 ft/min (adjustable).
4.Conveyor Frame
- Function: Supports rollers, belts, and motor; withstands load weight.
- Material: Steel (powder-coated), aluminum (light-duty), or stainless steel (washdown).
- Width: Load width + 4"–6" (e.g., 18" box = 24" frame).
- Height: 12"–36" (ergonomic for boxes, low-profile for pallets).
5. Side Rails
- Function: Guide loads, prevent derailment.
- Types: Fixed (1"–4" high), adjustable, or roller guides for delicate loads.
- Material: Steel, aluminum, or stainless steel.
6. Accessories
- Pulleys: Guide belts, maintain tension (e.g., crowned pulleys for flat belts).
- Sensors: Enable accumulation or flow control (photoelectric/proximity).
- Guards: Cover belts or drive shaft for safety.
- Supports: Legs/stands every 5–10 feet.
This is a roller conveyor system with side guide rails using round belt to drive conveyor rollers.
Design Considerations of Belt-Driven Roller Conveyor
1. Load Capacity
- Light-duty (<200 lbs): 1.5"–1.9" rollers, O-ring belts.
- Medium-duty (200–1,000 lbs): 2.5" rollers, flat belts or heavy-duty O-rings.
- Heavy-duty (>1,000 lbs): Rare; chain-driven or MDR preferred.
- Calculate total load per zone (e.g., 5 boxes × 50 lbs = 250 lbs).
2. Conveyor Layout
- Straight: Common for transport or accumulation.
- Curved: Tapered rollers with angled belts or line-shaft adjustments.
- Accumulation: Zoned belts with clutches or sensors for low-pressure queuing.
- Incline/Decline: Ensure belt grip and motor torque (e.g., 1 HP for steep angles).
3. Conveyor Speed
- Range: 30–150 ft/min (typical: 60–100 ft/min).
- Adjustable via VFD or motor pulley size.
4. Environment
- Dry/Indoor: Steel rollers, polyurethane belts.
- Washdown/Food-Grade: Stainless steel rollers, PVC or food-grade belts.
- Harsh (Dust, Oil): Sealed bearings, durable belts (e.g., rubber).
- Cold Storage: Low-temperature belts and motors.
5. Belt Tension and Maintenance
- Tension belts to avoid slippage but prevent overstretching.
- Design for easy belt replacement (e.g., accessible pulleys, removable guards).
- Inspect belts for wear or cracking every 3–6 months.
6. Safety Features
- Guards for belts and drive shaft to prevent pinch hazards.
- Emergency stops and overload protection.
- Side rails (2"–4" high) for load stability.
This is a flexilble powered roller conveyor using v-belt to drive conveyor rollers.
How to Choose a Belt-Driven Roller Conveyor
1. Define Application Requirements
- Load: E.g., 50-lb boxes (18" x 12") or 500-lb small pallets (40" x 32").
- Purpose: Transport, accumulation, or merging.
- Distance: E.g., 20' straight or 15' with 45° curve.
2. Select Roller and Belt Type
Conveyor Rollers
- 1.5"–1.9" for light loads (<200 lbs).
- 2.5" for medium loads (200–1,000 lbs).
- Spacing: 2"–6" (load spans 3+ rollers).
Driving Belts
- O-Ring (line-shaft): Light-duty, zoned control.
- Flat Belt (BDLR): Medium-duty, continuous drive.
- Material: Polyurethane (standard), PVC (food-grade).
3. Choose Drive System
- Motor: 1/2 HP (light), 1–2 HP (medium).
- Drive Type: Line-shaft with O-rings or direct flat belt drive.
- Controls: Basic (on/off) or PLC/sensors for accumulation.
- Speed: 60–100 ft/min, adjustable.
4. Determine Frame and Width
- Width: Load width + 4"–6" (e.g., 18" box = 24" conveyor).
- Frame: Steel for durability; stainless steel for washdown.
5. Factor in Environment
- Indoor: Steel rollers, polyurethane belts.
- Food-grade: Stainless steel, food-grade belts.
- Harsh: Sealed components, rubber belts.
6. Budget and Maintenance
- Cost: $1,500–$8,000 per 10'–20' section.
- Maintenance: Replace belts every 1–2 years; inspect pulleys quarterly.
Pricing of Belt-Driven Roller Conveyor
Belt-Driven Roller Conveyor
- Light-duty (24" wide, O-ring line-shaft): $1,500–$4,000 for 10'.
- Medium-duty (36" wide, flat belt): $3,000–$8,000 for 10'–20'.
- Example: 15' x 24" with accumulation ≈ $3,500–$6,000.
Key Components
- Rollers: Steel (1.9"): $5–$20 each; stainless steel: $15–$50.
- Belts:
- O-Ring (polyurethane): $1–$5 each (10"–24" loop).
- Flat Belt: $10–$50/ft (4"–12" wide).
- PVC (food-grade): $20–$100/ft.
- Pulleys: $10–$50 each (steel, crowned).
- Motor: 1/2–2 HP: $100–$500.
- Gearbox: $200–$1,000.
- Side Rails: Steel (2" high): $5–$20/ft; roller guides: $20–$100/ft.
- Sensors: Photoelectric: $50–$200 each.
- Spares: Budget $100–$300 for belts, rollers, pulleys per 10' section.
This is a flexible conveyor using O belt to drive conveyor rollers.
Maintenance Tips of Belt-Driven Roller Conveyor
- Belts: Inspect for wear, cracking, or stretching every 3–6 months; replace every 1–2 years.
- Rollers: Check bearings for noise or wear quarterly; replace if damaged.
- Pulleys: Ensure alignment; clean debris monthly.
- Motor/Gearbox: Service annually; monitor for overheating.
- Spares: Keep belts and rollers on hand to minimize downtime.
Comparison with Other Roller Conveyors
Types of Roller Conveyors | Pros | Cons | Best For |
Belt-Driven Conveyor | Quiet, smooth, low maintenance, cost-effective for light/medium loads. | Limited torque for heavy loads (>1,000 lbs), belts wear faster than chains. | Boxes, totes, small pallets, clean environments. |
Motor-Driven (MDR) Conveyor | Energy-efficient, precise (zoned control), no belts/chains. | Higher cost, less suited for heavy loads. | Automation, light/medium loads. |
Chain-Driven Conveyor | High torque, handles heavy loads (up to 5,000 lbs). | Noisy, high maintenance (chain lubrication). | Pallets, harsh environments. |
Example Specification of Belt-Driven Roller Conveyor
- Scenario: 20' belt-driven roller conveyor for 50-lb boxes (18" x 12") with accumulation.
- Width: 24" (18" + 6").
- Rollers: 1.9" steel, 3" spacing (box spans 6 rollers).
- Drive: Line-shaft, O-ring belts, 1 HP motor, 60 ft/min, low-pressure accumulation.
- Controls: PLC, sensors for zoned control (5' zones).
- Frame: Steel, 30" height.
- Side Rails: Adjustable steel, 2" high.
- Cost: $4,000–$7,000 (conveyor); $200–$400 (spares: 20 O-rings, 5 rollers, 2 pulleys).
Belt-driven roller conveyors are smooth, quiet systems for light to medium loads, costing $1,500–$8,000 per section. Key components include rollers ($5–$50), O-ring or flat belts ($1–$100/ft), and motors (1/2–2 HP). They're ideal for boxes or small pallets in clean environments. If you need a specific design, component focus (e.g., belt sizing), or pricing for a particular setup, share details (e.g., load, length, application), and I'll refine the response!
Leave Me Your Requirement!