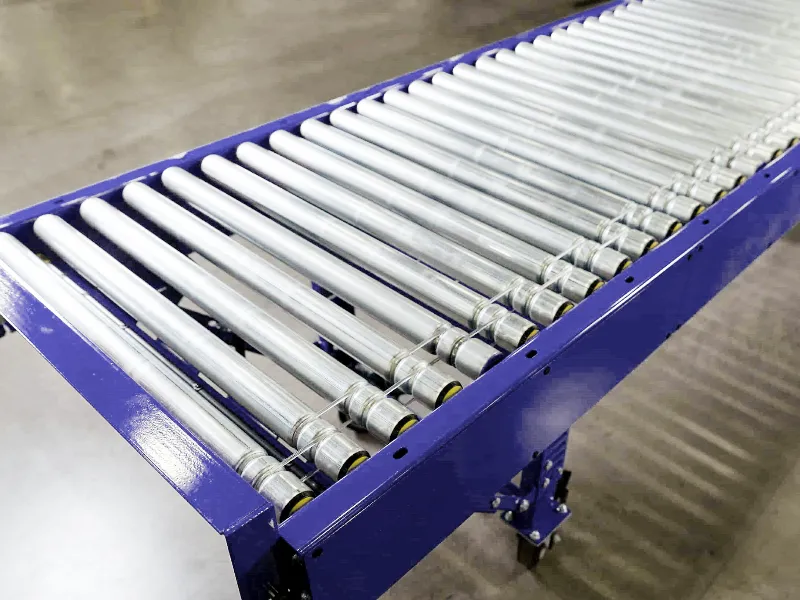
High Performance Motor Driven Roller Conveyor
These motor driven roller conveyors use rollers with internal motors or external motors to drive the rollers, offering precise control, energy efficiency, and suitability for automation.
What is a Motor-Driven Roller Conveyor?
A motor-driven roller conveyor (MDR) is a powered conveyor system where rollers are driven by motors to transport loads. Unlike chain-driven conveyors, MDRs often use rollers with internal motors (e.g., 24V DC) or external motors driving rollers via belts or chains. MDRs are known for their precision, low energy consumption, and ability to support zoned accumulation, making them ideal for automated warehouses, distribution centers, and light to medium-duty applications.Key Features of Motor-Driven Roller Conveyor
- Precision Control: Individual motorized rollers allow zoned operation (e.g., accumulation, sorting).
- Energy Efficiency: 24V DC motors consume power only when moving loads.
- Modularity: Easy to configure for straight, curved, or complex layouts.
- Low Maintenance: Fewer moving parts than chain-driven systems (no chains/sprockets in many designs).
- Applications: E-commerce, parcel handling, assembly lines, food processing, and automated systems.
Key Components of Motor-Driven Roller Conveyor
1. Motorized Rollers
Rollers with internal motors drive the load directly or power adjacent rollers.
Specifications
- Roller Diameter: 1.9"–2.5" (common for MDR); larger (3.5") for heavier loads.
- Voltage: 24V DC (standard); 48V DC for heavier applications.
- Power: 30–100W per roller (equivalent to ~1/20–1/10 HP).
- Material: Steel (galvanized), stainless steel (food-grade), or plastic-coated.
Drive Method:
Internal motor drives roller directly.
- O-rings, belts, or bands connect motorized roller to 2–10 adjacent rollers in a zone.
- Capacity: 50–1,000 lbs per roller (depends on motor and frame).
2. Non-Driven Rollers
- Support loads, driven by belts/bands from motorized rollers.
- Specifications: Match motorized roller diameter (e.g., 1.9"), with precision bearings.
- Material: Steel, stainless steel, or plastic.
3. Drive System
- Internal Motors: 24V DC motors inside rollers, controlled by driver cards.
- External Motors: Less common; AC motors (1/2–2 HP, 110V–480V) drive rollers via belts or chains.
- Driver Cards: Control each motorized roller or zone (e.g., speed, direction, accumulation).
Drive Controls
- PLCs for automation.
- Sensors (photoelectric/proximity) for zoned accumulation.
- Variable speed (10–150 ft/min).
4. Conveyor Frame
- Function: Supports rollers and load; houses wiring and controls.
- Material: Steel (powder-coated), aluminum (light-duty), or stainless steel (washdown).
- Width: Load width + 4"–6" (e.g., 18" box = 24" frame).
- Height: 12"–36" (low-profile for pallets, ergonomic for boxes).
5. Side Rails
- Function: Guide loads, prevent derailment.
- Types: Fixed (1"–4" high), adjustable, or roller guides for delicate loads.
- Material: Steel, aluminum, or stainless steel.
6. Accessories
- Sensors: Detect loads for accumulation or flow control.
- Cables: Connect rollers to driver cards (e.g., M8/M12 connectors).
- Guards: Cover wiring or motors for safety.
- Supports: Legs/stands every 5–10 feet.
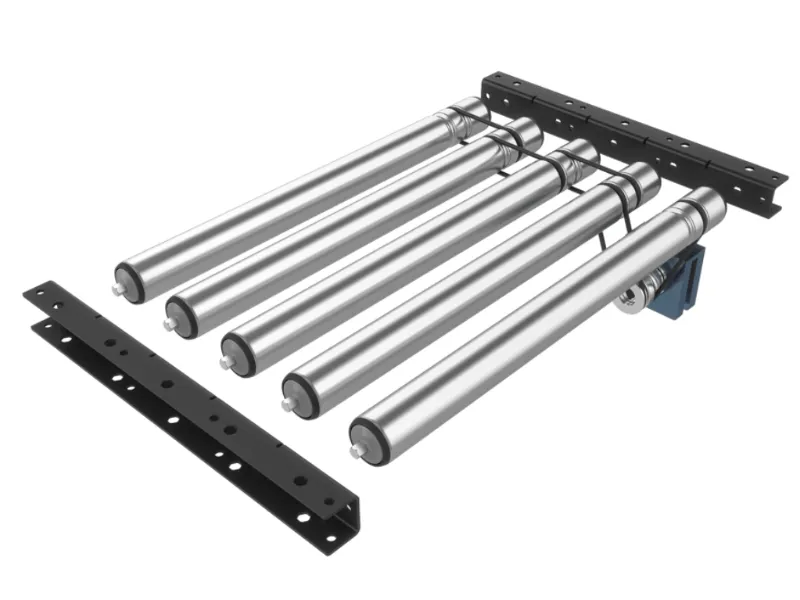
Design Considerations of Motor-Driven Roller Conveyor
1. Load Capacity
- Light-duty (<200 lbs): 1.9" rollers, 24V DC, 50W motors.
- Medium-duty (200–1,000 lbs): 2.5" rollers, 24V–48V DC, 75–100W motors.
- Heavy-duty (>1,000 lbs): External AC motors or reinforced MDRs (less common).
- Calculate total load per zone (e.g., 5 boxes × 50 lbs = 250 lbs).
2. Conveyor Layout
- Straight: Standard for transport or accumulation.
- Curved: Tapered rollers (1.9" inner to 2.5" outer) for smooth turns. The angles of the curved roller conveyor are 45 degrees, 90 degrees, and 180 degrees.
- Zoned Accumulation: 2'–5' zones, each with one motorized roller and sensors.
- Incline/Decline: Ensure sufficient motor torque (e.g., 100W for steep angles).
- Flexible: Our flexible roller conveyors ensure flexible conveying routes.
3. Conveyor Speed
- Range: 10–150 ft/min (typical: 30–60 ft/min).
- Adjustable via driver cards or VFD for external motors.
4. Environment
- Dry/Indoor: Steel or aluminum rollers/frames.
- Washdown/Food-Grade: Stainless steel rollers, IP65-rated motors.
- Cold Storage: Low-temperature motors (e.g., -20°C rated).
- Harsh: Sealed rollers, corrosion-resistant frames.
5. Zoned Control
- Divide conveyor into zones (e.g., 2'–5' long) for zero-pressure accumulation.
- One motorized roller per zone drives 2–10 non-driven rollers via bands.
- Sensors trigger stop/start per zone.
6. Safety Features
- Emergency stops, guards for wiring/motors.
- Side rails (2"–4" high) for load stability.
- Low-voltage (24V DC) reduces electrical hazards.
How to Choose a Motor-Driven Roller Conveyor
1. Define Application Requirements
- Load: E.g., 50-lb boxes (18" x 12") or 500-lb pallets (48" x 40").
- Purpose: Transport, accumulation, sorting, or merging.
- Distance: E.g., 20' straight or 15' with 90° curve.
2. Select Roller and Motor Type
Rollers
- 1.9" for light/medium loads (<500 lbs).
- 2.5" for medium loads (500–1,000 lbs).
- Spacing: 2"–6" (load spans 3+ rollers).
Motors
- 24V DC (internal): Light/medium, zoned control.
- AC (external): Heavy-duty or high-speed (less common).
3. Choose Control System
- Basic: On/off or fixed speed for simple transport.
- Advanced: PLC, sensors, driver cards for accumulation or automation.
- Speed: 30–60 ft/min, adjustable.
4. Determine Frame and Width
- Width: Load width + 4"–6" (e.g., 18" box = 24" conveyor).
- Frame: Steel for durability; stainless steel for washdown.
5. Factor in Environment
- Indoor: Standard steel rollers.
- Food-grade: Stainless steel, IP65 motors.
- Harsh: Sealed or corrosion-resistant components.
6. Budget and Maintenance
- Cost: $2,000–$10,000 per 10'–20' section.
- Maintenance: Inspect rollers/sensors quarterly; replace driver cards if faulty.
Pricing of Motor-Driven Roller Conveyor
Motor-Driven Roller Conveyor
- Light-duty (24" wide, 24V DC): $2,000–$5,000 for 10'.
- Medium-duty (36" wide, accumulation): $4,000–$10,000 for 10'–20'.
- Example: 15' x 24" with zero-pressure accumulation ≈ $5,000–$8,000.
Key Components
- Motorized Rollers: 24V DC, 1.9": $50–$200 each; 2.5": $100–$300.
- Non-Driven Rollers: Steel (1.9"): $5–$20 each; stainless: $15–$50.
- Driver Cards: $50–$150 each (1 per zone).
- Sensors: Photoelectric: $50–$200 each.
- Side Rails: Steel (2" high): $5–$20/ft; roller guides: $20–$100/ft.
- Cables/Connectors: $10–$50 per zone.
- Spares: Budget $200–$500 for rollers, driver cards, sensors per 10' section.
Maintenance Tips of Motor-Driven Roller Conveyor
- Rollers: Inspect for motor noise or bearing wear quarterly; replace if faulty.
- Driver Cards: Check for error codes; replace if malfunctioning (every 3–5 years).
- Sensors: Clean lenses, ensure alignment monthly.
- Belts/Bands: Replace if stretched or cracked (every 1–2 years).
- Wiring: Inspect cables/connectors for damage annually.
- Spare Parts: Keep motorized rollers and driver cards on hand to minimize downtime.
Example Specification
- Scenario: 20' motor-driven roller conveyor for 50-lb boxes (18" x 12") with accumulation.
- Width: 24" (18" + 6").
- Rollers: 1.9" steel, 3" spacing (box spans 6 rollers); 1 motorized roller per 3' zone.
- Drive: 24V DC, 50W rollers, 40 ft/min, zero-pressure accumulation (6 zones).
- Controls: PLC, photoelectric sensors, driver cards.
- Frame: Steel, 30" height.
- Side Rails: Adjustable steel, 2" high.
- Cost: $6,000–$10,000 (conveyor); $300–$600 (spares: 2 motorized rollers, 5 non-driven, 2 driver cards).
Comparison with Chain-Driven Roller Conveyors
Motor-Driven (MDR)
- Pros: Energy-efficient, quiet, precise (zoned control), low maintenance, no chains.
- Cons: Higher initial cost, less suited for very heavy loads (>1,000 lbs).
- Best For: Light/medium loads, automation, clean environments.
Chain-Driven
- Pros: Robust, high torque, handles heavy loads (up to 5,000 lbs), lower cost for heavy-duty.
- Cons: Noisy, higher maintenance (chain lubrication), less precise.
- Best For: Heavy pallets, harsh environments.
Motor-driven roller conveyors, typically using 24V DC motorized rollers, are precise, energy-efficient systems for light to medium loads, costing $2,000–$10,000 per section. Key components include motorized rollers ($50–$300), driver cards ($50–$150), and sensors ($50–$200). They excel in automated settings like e-commerce or food processing. If you need a specific design, component focus (e.g., motor sizing), or pricing for a particular setup, share details (e.g., load, length, application), and I'll refine the response!
Leave Me Your Requirement!