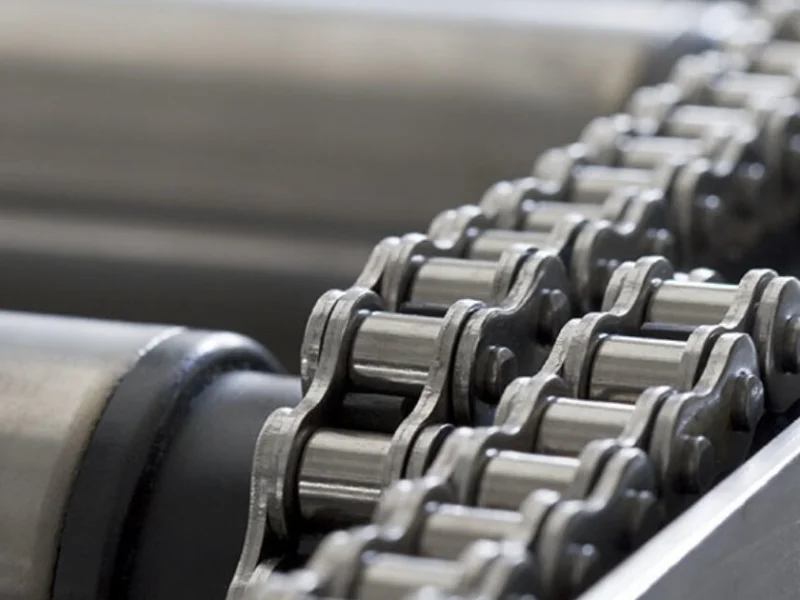
Long Lasting Chains for Sprocket Roller Conveyor
In a chain-driven roller conveyor, a roller chain transmits power from a motor to the rollers or between rollers to move loads. The chain engages sprockets attached to the rollers or a drive shaft, providing slip-free, robust power transfer. This makes chain-driven systems ideal for heavy-duty applications like pallet handling, industrial transport, or environments requiring durability.
Role of the Roller Conveyor Chain
- Power Transmission: Transfers rotational force from the motor to rollers via sprockets.
- Load Movement: Drives rollers to move items (e.g., boxes, pallets) along the conveyor.
- Durability: Handles high loads (up to 5,000 lbs+) and harsh conditions (e.g., dust, oil).
Types of Roller Chains for Roller Conveyors
1. Standard Roller Chain (ANSI)
Description: Most common, made of carbon steel, used in general industrial conveyors.
Sizes
- #40: 1/2" pitch, light/medium loads (e.g., boxes, totes, <500 lbs).
- #50: 5/8" pitch, medium/heavy loads (e.g., small pallets, 500–2,000 lbs).
- #60: 3/4" pitch, heavy-duty (e.g., large pallets, 2,000–5,000 lbs).
Larger sizes (#80, #100) for extreme loads.
Tensile Strength
- #40: ~3,700 lbs.
- #50: ~6,100 lbs.
- #60: ~8,500 lbs.
2. Stainless Steel Roller Chain
- Description: Corrosion-resistant, used in food-grade, washdown, or chemical environments.
- Sizes: Same as standard (#40–#60).
- Tensile Strength: Slightly lower than carbon steel (e.g., #50: ~5,000 lbs).
- Use Case: Food processing, pharmaceuticals.
3. Nickel-Plated Roller Chain
- Description: Carbon steel with nickel coating for moderate corrosion resistance.
- Use Case: Outdoor or mildly corrosive settings; cheaper than stainless steel.
4. Heavy-Duty Roller Chain
- Description: Thicker plates or reinforced design for extreme loads or high wear.
- Example: #60H (heavy series) for rugged applications.
- Use Case: Mining, heavy pallet handling.
5. Double-Pitch Roller Chain
- Description: Longer pitch (e.g., C2040, C2050) for slower, less frequent use.
- Use Case: Light-duty conveyors with wider roller spacing.
Key Specifications of Roller Chains
- Pitch: Distance between roller centers (e.g., 1/2" for #40, 3/4" for #60).
- Width: Inner width between plates (e.g., 5/16" for #40).
- Roller Diameter: Affects load capacity and smoothness (e.g., 0.312" for #40).
- Tensile Strength: Maximum load before breaking (e.g., 6,100 lbs for #50).
- Material: Carbon steel (standard), stainless steel (food-grade), or nickel-plated (corrosion-resistant).
- Lubrication: Pre-lubricated or requires periodic oil/grease application.
Roller Conveyor Chain Specifications
Parameter | #40 Chain | #50 Chain | #60 Chain |
Pitch (P) | 1/2" (12.7 mm) | 5/8" (15.875 mm) | 3/4" (19.05 mm) |
Roller Diameter (d1) | 0.312" (7.92 mm) | 0.400" (10.16 mm) | 0.469" (11.91 mm) |
Inner Width (b1) | 0.312" (7.95 mm) | 0.375" (9.53 mm) | 0.500" (12.70 mm) |
Pin Diameter (d2) | 0.156" (3.96 mm) | 0.200" (5.08 mm) | 0.234" (5.94 mm) |
Plate Thickness (T) | 0.060" (1.52 mm) | 0.080" (2.03 mm) | 0.094" (2.39 mm) |
Plate Height (H) | 0.472" (12.0 mm) | 0.591" (15.0 mm) | 0.709" (18.0 mm) |
Weight per Foot | 0.42 lbs/ft (0.63 kg/m) | 0.69 lbs/ft (1.03 kg/m) | 1.00 lbs/ft (1.49 kg/m) |
Parameter | #40 Chain | #50 Chain | #60 Chain |
Average Tensile Strength | 3,700 lbs (16.5 kN) | 6,100 lbs (27.1 kN) | 8,500 lbs (37.8 kN) |
Maximum Allowable Load | 810 lbs (3.6 kN) | 1,400 lbs (6.2 kN) | 1,980 lbs (8.8 kN) |
Operating Speed (Max) | 500 ft/min (152 m/min) | 450 ft/min (137 m/min) | 400 ft/min (122 m/min) |
Temperature Range | -10°C to 60°C (14°F to 140°F) standard; special chains up to 200°C (392°F) | ||
Lubrication Requirement | Periodic (every 100–500 hours, SAE 20 oil or grease) |
How to Choose a Roller Chain for a Roller Conveyor
1. Determine Load Requirements
- Weight: Match chain to maximum load per roller or zone.
- Light loads (<500 lbs): #40 chain.
- Medium loads (500–2,000 lbs): #50 chain.
- Heavy loads (2,000–5,000 lbs): #60 or larger.
- Example: A 1,500-lb pallet needs #50 or #60 chain with >6,000 lbs tensile strength.
2. Assess Roller and Sprocket Compatibility
- Rollers (e.g., 2.5" diameter) need sprockets matching chain pitch (e.g., #50 sprocket with 10–20 teeth).
- Ensure sprocket bore fits roller axle (e.g., 1/2"–1" diameter).
3. Consider Conveyor Environment
- Dry/Indoor: Carbon steel (#40–#60, $0.50–$3.50/ft).
- Wet/Food-Grade: Stainless steel ($3–$10/ft).
- Corrosive/Outdoor: Nickel-plated ($1–$5/ft).
- High Wear: Heavy-duty or sealed chains.
4. Calculate Chain Length
- Measure the loop length (e.g., 10' conveyor may need 20' chain for drive and return).
- Add extra for tensioning (e.g., 2–5% slack).
- Example: 15' conveyor ≈ 30'–32' chain.
5. Select Motor and Speed
- Chain speed (30–60 ft/min) depends on motor (1/2–5 HP) and sprocket size.
- Smaller sprockets increase speed but reduce torque; larger sprockets suit heavy loads.
6. Factor in Maintenance
- Lubricate every 100–500 hours (e.g., SAE 20 oil or grease).
- Choose sealed or low-maintenance chains for harsh environments.
Pricing for Conveyor Roller Chains
Based on data from sources like Made-in-China.com, eBay, and suppliers (e.g., Grainger, Tsubaki):
Standard Roller Chain (Carbon Steel)
- #40: $0.50–$1.50 per foot.
- #50: $1–$2.50 per foot.
- #60: $1.50–$3.50 per foot.
- Example: 30' of #50 chain ≈ $30–$75.
Stainless Steel Chain
- #40: $2–$5 per foot.
- #50: $3–$7 per foot.
- #60: $5–$10 per foot.
- Example: 30' of #50 stainless ≈ $90–$210.
Nickel-Plated Chain
- #50: $1.50–$4 per foot.
Bulk Rolls
100' rolls reduce costs (e.g., #50 carbon steel: $100–$250).
Sprockets
$5–$50 each (e.g., #50, 15-tooth steel: $10–$20).
Replacement Costs
udget $100–$500 for chain/sprocket replacements per 10' conveyor section every 1–5 years.
Design Considerations for Chain-Driven Roller Conveyors
1. Chain Layout
- Single Chain: One chain drives multiple rollers via sprockets (common for light/medium loads).
- Dual Chain: Two chains per roller for heavy loads (e.g., pallets).
- Zoned: Separate chain loops for accumulation zones with clutches or sensors.
2. Tensioning System
- Use adjustable idlers or spring-loaded tensioners to maintain chain tautness.
- Avoid over-tensioning (causes wear) or under-tensioning (causes slippage).
3. Chain Guard
- Steel or plastic cover over chain to protect operators and prevent debris.
- Design for easy removal during maintenance.
4. Roller and Frame
- Rollers: 2.5"–3.5" diameter, steel, spaced 3"–6" for pallets/boxes.
- Frame: Steel, reinforced for heavy loads (e.g., 1,000–5,000 lbs).
5. Safety Features
- Emergency stops and overload sensors prevent chain breakage.
- Side rails (4"–6" high) stabilize loads.
Maintenance Tips for Roller Chains
- Lubrication: Apply oil/grease every 100–500 hours; use food-grade lubricants for sanitary settings.
- Inspection: Check for wear, elongation, or broken links monthly; replace if chain stretches >3%.
- Tension: Adjust to remove excessive slack (e.g., 1–2% of chain length).
- Cleaning: Remove debris in washdown environments; avoid water on carbon steel chains.
Example Selection
- Scenario: A 10' chain-driven roller conveyor for 1,000-lb pallets (48" x 40").
- Chain: #50 carbon steel (5/8" pitch, ~6,100 lbs strength).
- Length: ~20' chain (10' conveyor + return loop).
- Sprockets: #50, 15-tooth, steel, one per roller.
Cost:
- Chain: 20' × $2/ft = $40.
- Sprockets: 10 rollers × $15 = $150.
- Total: ~$190 (chain/sprockets only; conveyor ~$5,000–$8,000).
Roller chains for chain-driven roller conveyors are critical for heavy-duty transport, with #40–#60 chains costing $0.50–$10/ft depending on material. Selection hinges on load (light to heavy), environment (dry, wet, corrosive), and maintenance needs. For a precise chain specification or conveyor design, share your load weight, conveyor size, and application details. If you meant something specific (e.g., chain maintenance, a different conveyor type), let me know, and I'll adjust the response!
Leave Me Your Requirement!